Battery / High Power Ultrasonic Bonders
Ultrasonic welding equipment for the production of battery packs, power electronics and other applications, from manual tabletop to full automatic in-line, we also offer local bonding services.
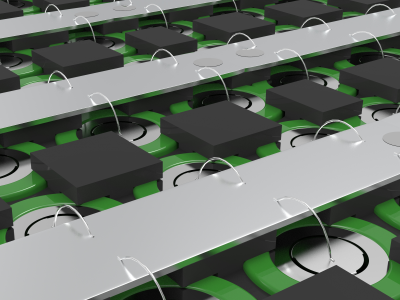
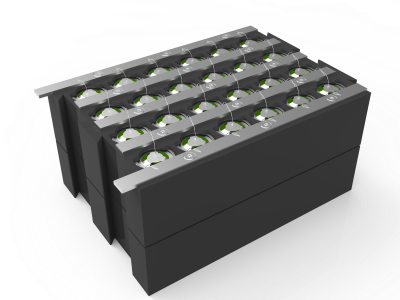
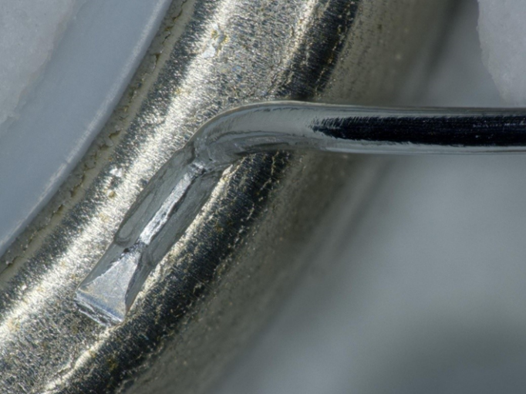
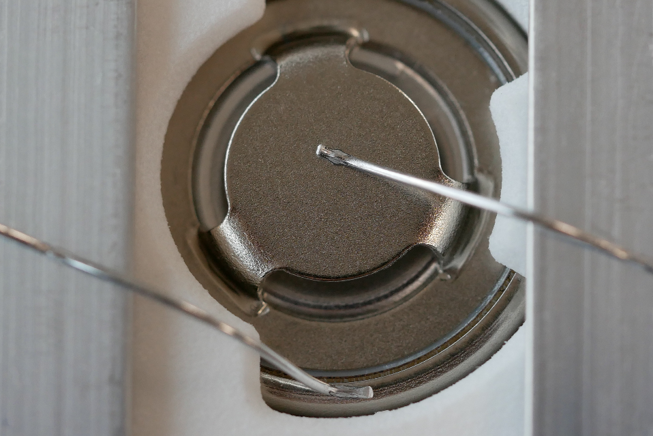
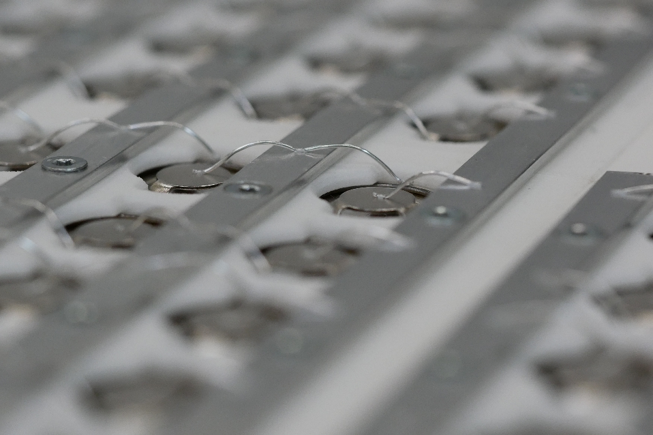
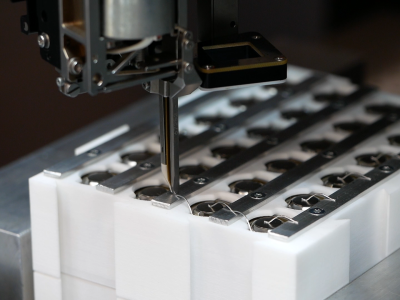
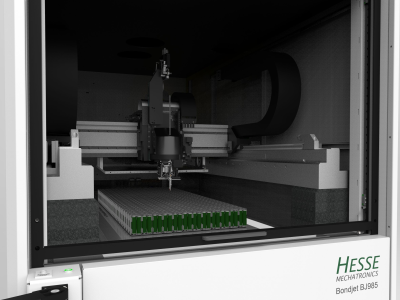
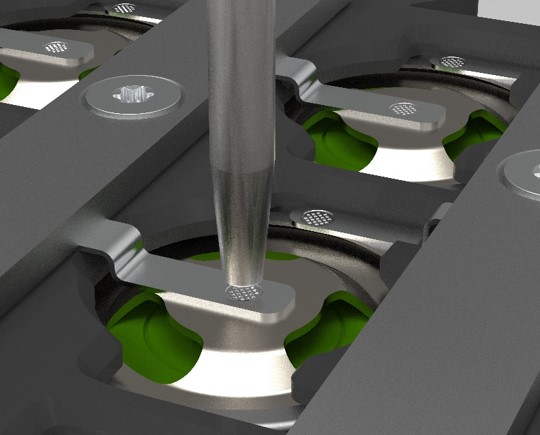
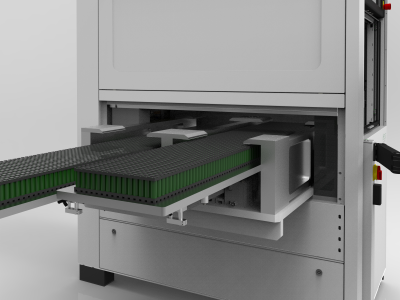
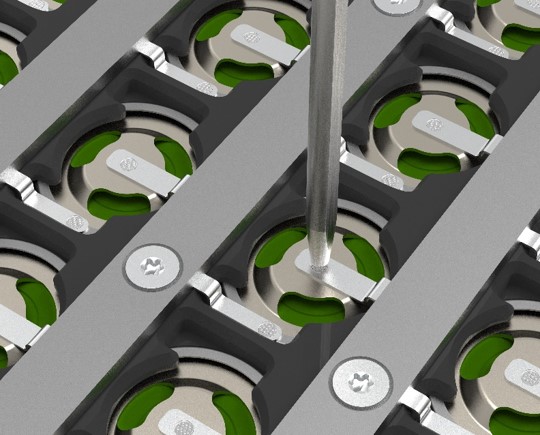
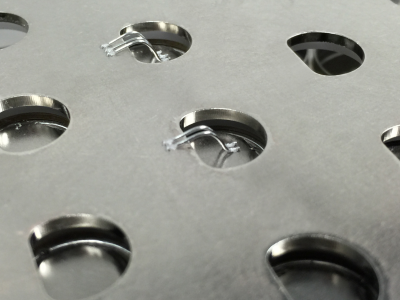
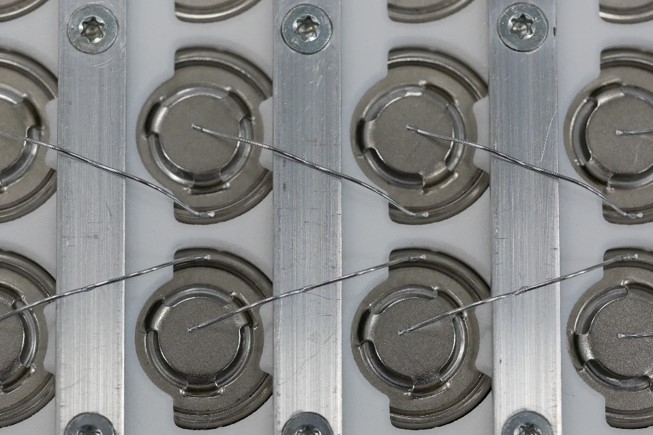
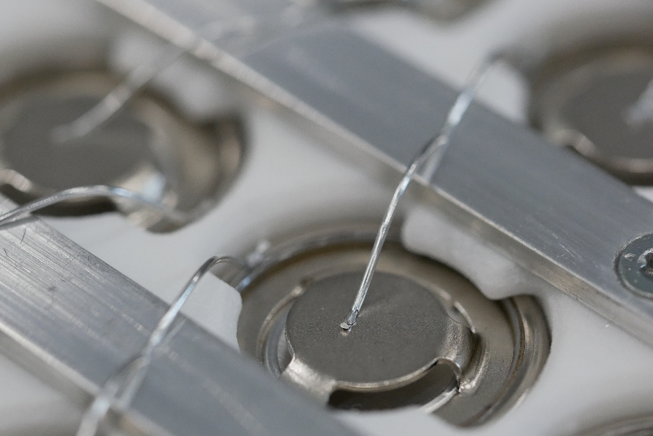
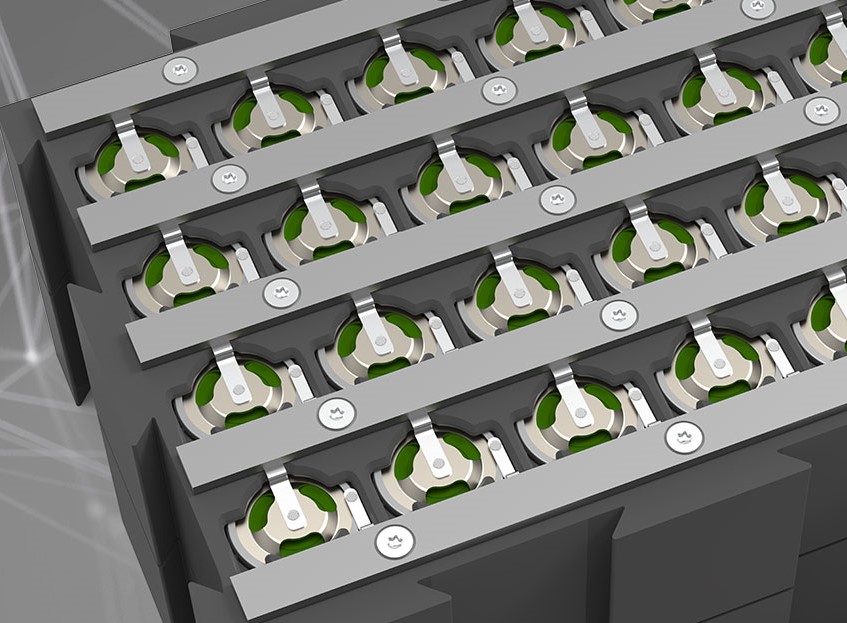
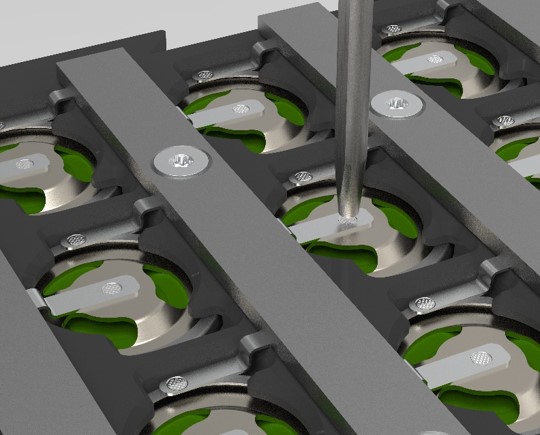
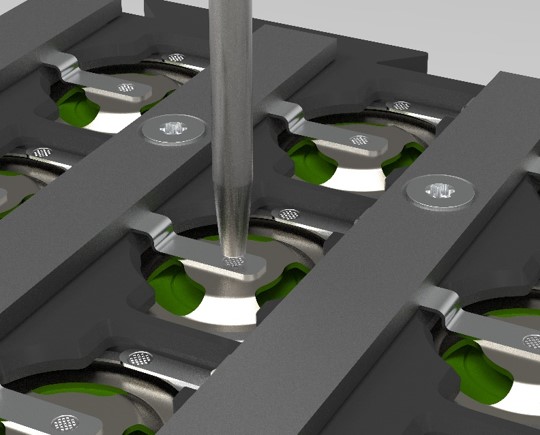
Introduction of Ultrasonic Wire Bonding for Batterypacks
Wire bonding (ultrasonic compression bonding) is a combination of three precisely controlled parameters that form the bond: (i) Ultrasonic vibrational power; (ii) Downwards force; and, (iii) Time. The wire is pushed with a controlled force against the surface to be bonded, then the wire is vibrated (in battery production this typically happens at 60kHz for 100 milliseconds).
Each wire has at least two bond locations – the first bond (source) and the second bond (destination) – but chain or stitch bonds with multiple bonds per wire can be created too. The wire or ribbon forms a loop between the bond locations, compensating thermomechanical stress.
Wire sizes from 15μm to 650μm can be processed resulting in a wide field of applications in the sector of volume production but especially in globally scaling mass production of semiconductor and sensor products. The industry distinguishes between fine and heavy wire bonding: fine wire (<100μm) is processed for low current applications (camera chips, sensors or high frequency applications), while heavy wires (≥100μm) are more suitable for batteries and power applications, e.g. inverters, switching devices or control units. Power applications typically use 75μm up to 650μm aluminium wire, but copper wire or ribbon can also be processed.
Advantages of Wire Bonding vs Spot or Laser Welding
Fusing Wires: Wire acts as a fuse. If a cell fails, it is isolated from the battery pack, allowing the remainder of the pack to continue to function as required. Thus, the pack is not destroyed by a meltdown and can be fixed at a convenient later date, ensuring no danger to life from a simple cell failure.
No Heat: Heat is dangerous for an 18650 cell and this requirement is met through the technique of wire bonding. Unlike other methods such as spot or laser welding, no heat is used in ultrasonic compression bonding. The only heat produced is localised and generated as a by-product of the friction required to make the bond. This temperate change is restricted to the outer skin of the surface only, making wire bonding ideal for work on cells which require the absence of heat.
Traceability of Each Bond: Process integrated Quality Control (PiQC) is provided in the form of a sensor integrated into the Transducer. This cutting edge and industry leading approach provides a multi-dimensional signal analysis of the bond process which calculates a bond quality index value in real-time. Using significant signals from the wire bonding process, the user is provided with instant feedback on the bonding process, ensuring high quality yields.
Clean Process: Wire bonding is a clean process. It generates no sparks, residue materials or other possible contaminations, saving time as subsequent clean-up requirements become unnecessary.
Height: Wire bonding machines are capable bonding in height variations. This means that battery packs which require variations in height for the cell and busbar can be accommodated. Our machines also provide the user with full control over the design of the final loop shape, adding additional flexibility for unique application requirements.
Testability: Ensuring the highest quality requirements, wire bonds are easily tested for reliability on bond strength. This is harder to do when using an application technique such as spotwelds which are notoriously hard to test and known industry wide for their loss of connections.
Flexibility: Wire bonding offers flexibility in the bonding process due to the wire-loop shape and material properties. For products where a certain amount of pack malleability is required – where the pack may be exposed to a certain amount of flex – damage is unlikely to take place. This is a flexibility not shared with spotwelded packs which are more rigid in form, rendering the connections easier to break following movement.
Automation: Wire bonding allows full automation of the bonding process with CNC machines for higher efficiency and quality. In turn, this decreases the amount of manual labour required for system use.
Materials for Busbars
Busbars are used to connect the cells together in series. The question central to discussions surrounding busbars, is what conductive material (sheet metal) is best suited to the required application? We consider here the selection of Nickel, Copper or Aluminium, each suited to accommodate varying customer and application requirements.
Mechanically, busbars for the battery pack of EVs/HEVs must be durable, capable of withstanding high levels of vibration, while simultaneously providing rigidity. Combined, these maintain the integrity of the battery module assembly, essential requirements for many of our customer requirements.
Electrically, connections must handle both the high current resulting from the processing of the cells, in addition to the increasing voltage levels resulting from growing technology requirements, as cells of the future will be up to 5.0V per cell. This is an important step in the production process, as the potential impact on the clearance and creepage distance for the electrical insulation could be significant. Influencing the integrity of the end product further, is the composite materials used to construct the busbars themselves. For example:
- Nickel is not ideally suited for electrical conduction. Its historical use was valuable as it allowed for users to easily automate spotwelds. When it comes to conducting high current, aluminium and copper offer better results.
- Copper offers the best electrical conductivity, the greatest thermal conductivity and lowest thermal expansion, so for applications where these elements are key, copper may offer the best solution for busbar composite material. Despite these clear benefits, copper is fast to oxidise when exposed to air which can result in a negative effect on the quality of bonding and cell bond-ability.
- Aluminium is more than twice as conductive Nickel and less sensitive to oxidation. It is also less costly and lighter in weight than Copper. This means that for many customers, Aluminium is the best overall choice for their application requirements.
Fusing Current Bonding Wires
The fusing behaviour of Aluminium wire depends mainly on the diameter and length of the wire.


*Table credit: Heraeus bonding wires datasheet
Accelonix Services
Hot news
Our Partners
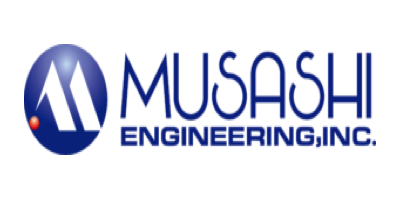
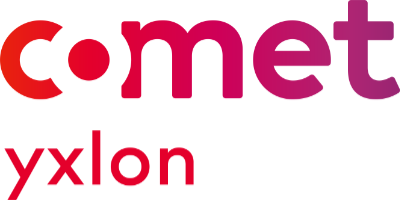
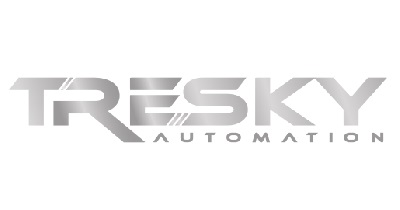
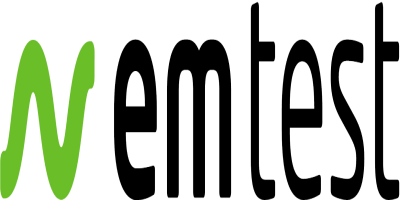

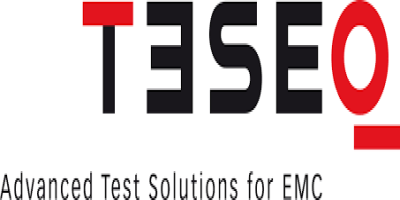
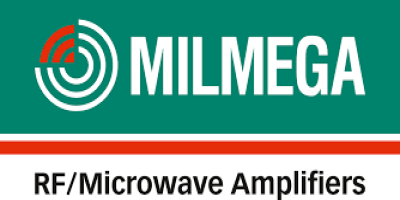
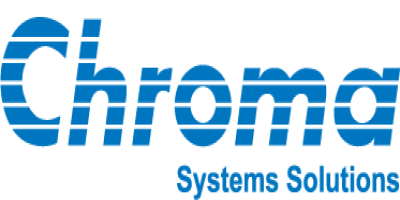
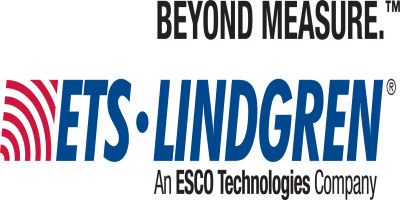
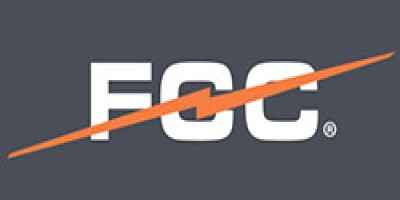
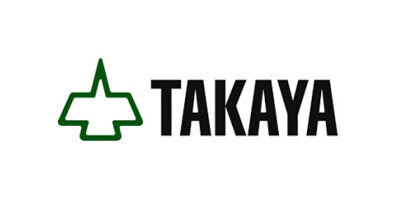

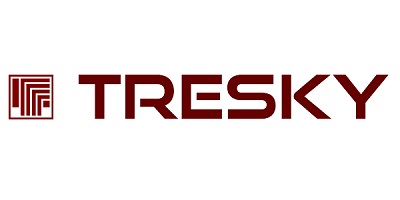
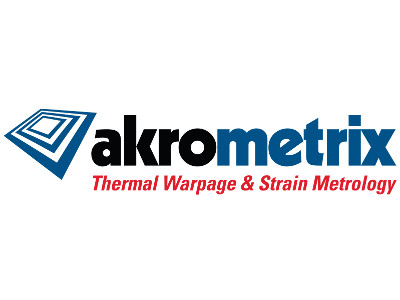
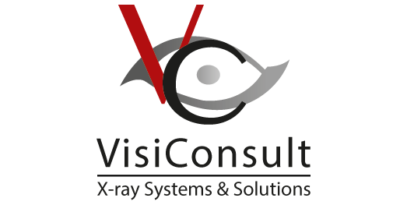
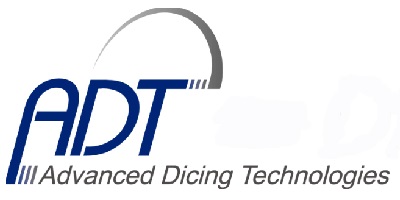
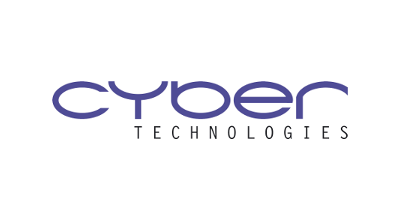
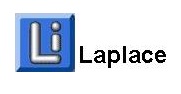
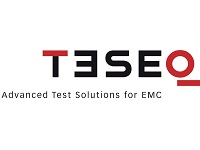