Hesse Mechatronics Smart Welder SW985 combines the best of two technologies: ultrasonic welding & wire bonding
- The force and ultrasonic power of ultrasonic welding equipment
and
- The flexibility, precision, speed and advanced process control features of wire bonding machines.
Smart Welder provide producers of medium-sized ultrasonically welded connections with increased process control and freedom of design for the next generation of capable, efficient and cost-effective designs in power electronics, battery packs and other applications.
The new Smart Welder by Hesse include precise positioning and rotation between welding tool and product, image recognition to detect the exact weld location, and derivation of an optimal trajectory to reach the weld location quickly and very precisely.
Together with long and narrow welding tools, this allows very tight spacing and thus compact products, higher power density.
Further advanced functions include touchdown sensing, precise and dynamic contact force control, diverse process control features such as monitoring of ultrasound characteristics and deformation (cf. DVS 2811), and standardized interfaces for assembly line integration.
Smart Welder can, like ultrasonic wire bonders, flexibly handle a large variety of products. New products only require a program change and possibly adapted clamping and automation.
PiQC – Process integrated Quality Control
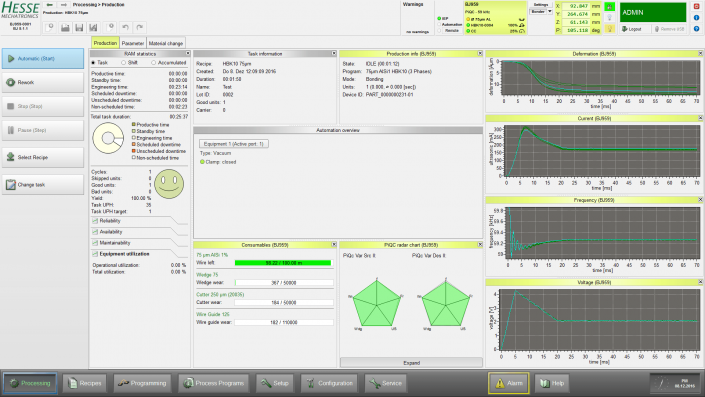
The Hesse GmbH has implemented a new Process integrated Quality Control system (PiQC) that is unique to the global wire bonding market. A sensor integrated into the transducer allows for the first time a multi-dimensional signal analysis of the bond process. PiQC calculates a bond quality index value in realtime, using significant signals from the wire bonding process.
Advantages for volume production
- Inspection of every bond
- No mechanical load of the bond connection
- Product specific configuration of the quality control system
Feedback from the process
- Mechanical oscillation of the wedge
- Friction at bond surface
- Transducer current
- Ultrasonic frequency progression
- Wire deformation
Quality statements by PiQC
PiQC calculates a quality index for each bond based on the actual feedback signal from the process.
The signal related components of the quality index can be displayed graphically at any time.
Teach mode for reference data
- Detailed automatic analysis of the welding process
- Extraction of process-specific reference data
Automation Solutions
The precise and safe handling of the products in and out of the production machine plays a significant role in controlling the product quality, yield and efficiency of the production equipment. For this reason Hesse GmbH is offering automation concepts individually adapted for every application.
Transport system
Transport system
All machines of Hesse GmbH can be equipped with a standard transport system or a customized version for a fully automated manufacturing in production lines or cells. In addition to single products and/or multi panels also Auer boats or other kind of product carriers can be used on the transport lane. As a service, the Hesse GmbH provides the design and manufacture of customized product carriers.
Basic design
- Transport system consisting of one segment with a bonding station
- Manual adjustable transport rail width
- Transport direction is from left to right
- Product detection by sensors
- Belt drive with stepper motor (belts antistatic coated)
Optional
- Transport system e.g. with 3 segments: Input buffer, bonding station and output buffer (Input and output buffer can also be used as preheat station or postheat station to cool down slowly)
- Transport systems with 2 or 3 lanes for parallel processing and transportation of products
- Dual lane system with shuttle transport for parallel using of several bond stations
- Additional bypass lane through the machine to increase the line availability at maintenance work or to optimize the index times for production cells with more machines
- Automatic adjustable rail width of the transport lane
- Linear drive with gripper for high throughput
- „Walking beam“ for Auer boats or product carriers
Magazin lifts
Magazine lifts
All machines of Hesse GmbH can be equipped with magazine lifts for the setup of manufacturing cells or islands. Our standard solution consists of simply attached lifts to the transport system, with the advantage of a cost-effective solution and optimum footprint.
Basic design
- Integrated width adjustable magazine lifts each for 1 magazine up to max. 18 kg
- Pusher for loading and unloading of products
- Magazine detection
Optional
- Short-pusher version with press rollers on the transport system
- Belt drive in the magazine for transfer to the transport system
- Slot monitoring at the magazine
- Magazine clamping
- Integrated lifts with capacity for several magazines
- Material handling systems with several lanes
- Stand-alone-lifts
Bonding Station
Bonding station
The core piece of the automation in the Hesse GmbH machine is the bonding station with its individual design layout and clamping principle. In general, the bonding station is disconnected from the transport system to prevent external influences and to ensure optimal bonding conditions. For different products or product carriers standard solutions have been developed, based on this special solutions can be developed.
Basic design
- Lifting cylinder with position monitoring
- Clamping with vacuum and vacuum monitoring
- Offbond station
Optional
- Vacuum and mechanical clamping
- Bonding station with heating to 250°C
- Vacuum monitoring and circuit in separate circles
- Tool-less quick-change system for product clamping
- Additional heated bonding station incl. vacuum sensor
Visualization
Visualization
By default, the operation of the automation of Hesse GmbH occurs via the machine interface including graphical representation of the current process state. In addition, an optional touch screen for complex automation systems and solutions are used with extended capabilities. Using a graphical user interface the production and setup can be visualized with manual control.
Visualization in automatic operation / production mode:
- Display of the machined magazine slot
- Display of the transport segment (preheating, bonding station, etc.) in which the product is located currently
- Scanned barcode of the product; such as scanning order data
- Temperature of heating (with monitoring function of the target state)
Visualization and control in manual setup / setup mode:
- Current status of the sensors
- Position of the axes
- Manual control of the entire automation system (e.g. motion of the bonding station, and/or operation of the vacuum)
MES Interface
MES Interface
We are able to realize a connection to any MES (Manufacturing Execution System). Product information such as bond program or rework data are determined and process results are returned for every product. The setup condition of the machine can be validated and parameters of automation can be received. MES connections are always realized as customer specific solutions.
Examples / options for MES-interfaces:
- Connection to customer database
- Connection to existing systems or MES server (such as iTAC)
- Development of customized solutions
- Individual solutions for connection to SECS / GEM host
Smart Welder SW985 Datasheet 