Industry 4.0 promotes what has been named “smart factory”. Within the modular structured smart factories, cyber-physical systems monitor physical processes, create a virtual copy of the physical world and make decentralized decisions. The key principles in Industry 4.0 are:
- Interoperability: Connect machines, devices, sensors and people to communicate with each other.
- Digital Simulation: Create a virtual copy of the physical world. Play with “What-if” scenarios in the virtual world in order to identify the optimized physical flow. Use theoretical results to control the physical world.
- Convert data into information: Aggregate raw data from cyber-physical systems to build and visualize comprehensive information that allow humans to make decisions based on facts.
- Decentralized decisions: the ability of cyber physical systems to make decisions on their own and to perform their tasks as autonomously as possible.
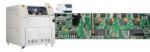
The Flying Probe Testers APT-1400F and APT-1600F are prepared for operation in the Industry 4.0 environment.
- Interfacing with other inline equipment is not only possible via legacy SMEMA connection, but also new interfaces for M2M communication are supported, eg SEMI A1.
The new communication interfaces allow inline product and product information exchange between machines over TCP/IP to make the assembly line operate in a smarter way. - The powerful twExpress software allows to simulate the test coverage result of the Takaya Flying Probe Test and optimize the complete test strategy for the PCBA, taking into account other inspection and test techniques such as Solder paste Inspection, AOI, JTAG/Boundary Scan and others.
This allow the user to make informed decisions on the distribution of test coverage prior to start the test development.
The twExpress software automatically optimizes the Takaya test, in terms of test coverage and according test cycle time. - The QUAD software finally complements the toolsuite by automated reading and archiving the Takaya test data and fault tickets into a comprehensive database. The QUAD tool not only harvests information from the Takaya tester, but also a wide range of other test and inspection machines are supported.
With power full reporting possibilities, the testdata is turned into dashboards, clear and readable analysis graphics and even real time process information.
Repair and rework cycles are shortened through an optimised repair station software that offers the operator a complete view on paperless repair tickets, combined with CAD data information and views as well as a diagnostic aid that uses an algorithme to propose repair solutions based on historic data. - To close the loop and ensure the test program integrity over long term, the twExpress software allows to regularly compare the test programs running on the production line to be compared with the originally generated test programs. In order to discover anomalies introduced over time and prevent test parameter degradation and loss of test coverage.
Please contact us for more information