T-5300-W
Manual Die Bonder with semi . process capabiltities
Wafer Handling capabiltities
Pick up from waffle, Gelpak or other.
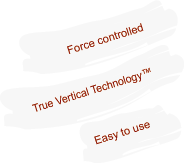
Tresky’s T-5300-W is the flagship of our Die Bonders and adds a motorized, programmable Z-axis, with our True Vertical Technology™, to the repertoire of the universal T-5100, making it extra useful for repetitive processes in small-scale production, where operator influence must be minimized. The T-5300 really shines in applications with highest precision requirements, such as flip-chip, or eutectic placement. An optional high-resolution beam splitter unit allows sub-micron placement accuracy.
The systems can run all basic functions as well as the industries most advanced applications by adding a wide range of available options. As with all of Tresky’s products, the T-5100-W incorporates True Vertical Technology™ which guarantees parallelism between chip and substrate at any bond height. Together with superior ergonomics the platform is the industry’s most sophisticated system in its class and with the new intuitive software even easier to operate.
The extremely rigid machine, with its completely redeveloped base is compact and fits on a lab desk. It can be expanded with many different modules to cover an enormous range of applications.
Operating a Tresky die bonder/placer is intuitive. A few minutes’ training is sufficient to start working with the machine. The accuracy and repeatability of placing parts is superb thanks to a number of well thought out features like a true, linear Z-Axis, Force Control, XY Fine Control and high-resolution optics that allow flip-chip placing down to sub-micron accuracy.
Typical and customized applications :
- Die sorting from wafer into waffle packs or gel packs
- Die attach with adhesive (stamped or dispensed)
- 3D packaging of MEMS, MOEMS, Photonics, …
- High-precision placement with visual adjustment by beam-splitter unit for look-up inspection of edges, corners or patterns, e.g. for laser bars
- Flip-Chip with ultrasonic die attach
- Flip-Chip with adhesives or anisotropic foils
- Sensor assembly
- UV curing of die attach
- Eutectic bonding of AuSi, Copper Pillar and others
- Ultrasonic bonding on a curved surface