Batenburg Industriële Elektronica is part of Batenburg Techniek, a Dutch technical service provider in the field of smart industry. The subsidiary is located in Neede, Netherlands, and focusses on assembly of industrial electronics. Batenburg decided to purchase an SPI system in order to ensure the highest quality of its electronic products at an early stage. The choice fell on the SPI · Line 3D from GÖPEL electronic in cooperation with the sales and service partner Accelonix.
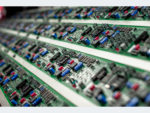
About 100 employees are involved in production, testing and assembly of high reliability electronic products. As a specialized EMS company, Batenburg Industriële Elektronica ensures customers of full support during the long product life cycles of their products. That means that Batenburg supports their customers by applying Design for Excellence (DFX) principles and provides engineering support during PCBA design. This includes optimization of PCBA designs for manufacturing, assembly and test, as well as management of the entire life cycle.
Products and Manufacturing
The products manufactured by Batenburg are mostly used in Aerospace, Industrial, Medical and Automotive industries. The production environment has a high mix profile – from prototypes and small series of 5 pieces up to volumes of 10.000 per batch. This high diversity is only possible with a flexible production process and up to 6 line changes during 2 shift workdays.
The PCBA production process is fully ISO certificated and involves SMT assembly, THT assembly (Through-hole Technology) and more specialized process services such as coating and potting.
For SMT assembly, Batenburg operates two production lines. A flexible semi-automated Mycronic Pick & Place line is being used for prototyping and small volume assembly. Larger volumes are processed on the fully automated Fuji line.
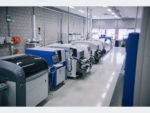
Quality Assurance
The PCBA’s produced by Batenburg need to comply with high quality Aerospace and Automotive standards. “Our ultimate goal is a zero defects process, but the first target is cost of error minimization in order to remain competitive and assure customer satisfaction” says René Temmink, Director Operations at Batenburg. To offer the customer highest test coverage, almost all available test and inspection technologies are integrated into the production lines: SPI (Solder Paste Inspection), AOI (Automated Optical Inspection), MXI (Manual X-ray Inspection), Flying Probe Test, In-Circuit-Test as well as Functional PCBA and End-of-Line test.
Solder Paste Inspection to detect faults at the earliest stage
It is still a fact that paste deposition defects are the biggest cause for soldering defects later in the assembly process. During solder paste inspection, assemblies with detected solder paste defects are sorted out after paste printing. This avoids unnecessary costs due to component assembly, especially in cases where defective assemblies are not repaired but disposed of. In the case of a serial error due to a clogged screen, countermeasures can be taken at an early stage. In the purchasing process Batenburg made comparative tests with different manufacturers of SPI systems. Defect detectability, user interface, ease of programming and availability of support were the main parameters. Furthermore the SPI system should be future proof. The final decision was made in favor of GÖPEL electronic SPI Line · 3D, as it performed favorably in the comparative testing compared to other solutions. The already long-term positive experience with the existing GÖPEL electronic AOI systems “Basic Line” and “Turbo Line” also influenced a positive decision. The transparency of the information during the benchmark and a look behind the scenes of the GÖPEL electronic organization and production of the inspection systems were also very convincing.
“GÖPEL electronic offers a comprehensive line up of inspection solutions. Standardization towards one supplier makes daily work easier for our organization and operators” states René Timmink.
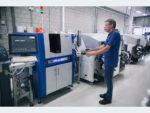
The main target of the SPI · Line 3D is to control the screen-printing process and to avoid paste defects, but the system does not only control the position of the solder paste. It also measures the deposit volumes and volume distribution. In a later stage and within the Industry 4.0 philosophy, the SPI · Line 3D will be operated in closed loop with the DEK screen printer. This will enable real-time automatic adjustment of the printing process and trigger dynamic maintenance cycles on the DEK screen printer.
Batenburg is very pleased with the support and service of both Accelonix and GÖPEL electronic.
The transparent communication between the three companies results in very efficient cooperation with fast response times, fast delivery of spare parts and a very high service level.
René Timmink on the cooperation: “The GÖPEL inspection systems matches very well with the requirements from Batenburg and the transparency of information. The development roadmap for future inspection solutions from GÖPEL is looking very promising. We look to further extend our cooperation in a mutually beneficial way for a “Smarter Focus and a Brighter Tomorrow”!”