The TAKAYA APT-1400F is the fastest flying probe test system in the world and sets new standards in speed and test coverage for the competition.
The system has been specially developed for the test of complex circuit boards and large quantities. The APT-1400F has 6 flying probes, of which 2 are vertical probes that enable accesses to contact points that could not previously be reached.
The APT-1400F does not make any compromises between speed, reliability and long service life. The design of the XY table has been completely revised and optimally adapted to the high travel speed of the test probes and to the new mechanical design of the axes. An outstanding measurement unit and numerous innovative test algorithms enable significant increase of the test coverage on your circuit boards.
Goepel Takaya Boundary Scan Integration 
TestWay Express is a fully integrated solution that enables electronic manufacturers to optimize the design to delivery flow by: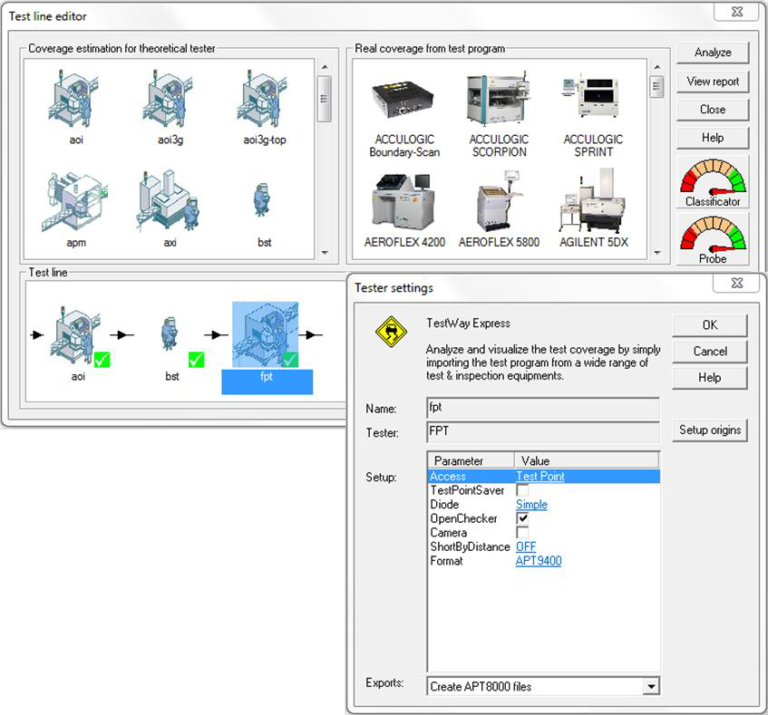
- Defining the manufacturing line; including a combination of assembly, inspection and test machines.
- Placing test probes intelligently to maximize the coverage and minimize the fixture costs, both initially and in the event of required modifications.
- Estimating the test coverage for each individual strategy using theoretical models and optimize the combined results.
- Generating input files for each test stage that reflects the test options for the selected strategy.
- Measuring the real test coverage by importing the post-debug test program or coverage data.
- Comparing the early estimation with the actual measured test program coverage, identifying gaps in the overall strategy.
The capability to generate lean test programs has particular benefits for the Takaya flying probe tester by:
- Reducing debug time: Machine capability models, automatic test creation algorithms, optimum probe angle selection methods and advanced circuit analysis work together to reduce the amount of machine debug time required after output, thereby increasing machine capacity.
- Increasing Test coverage: Push through technology allows automatic simple cluster testing to increase test coverage through low value resistive components.
- Reducing engineering effort: Automatic component modelisation and intelligent opportunity assessment work together to save engineering time.
- Increasing machine speed: Advanced circuit analysis algorithms allow the creation of tests to target the failure opportunities with no superfluous tests.
- Reducing machine workload: Powerful test coverage analyzers work within the machine capability models to allow the optimization of combined tests across multiple machines, in order to achieve a lean test strategy.
Click here for more information.