Flatness Measurement and Analysis Technique
The Digital Fringe Projection (DFP) technique compliments the shadow moiré technique by adding step height measurement capabilities at high data point density. This technique is particularly useful for measurement of connectors, sockets, assembled modules, and PCB local areas.
No grating is needed for the DFP technique, which helps with issues like outgassing and temperature uniformity sometimes seen with the shadow moiré technique. DFP also has the advantage of not being limited by data density, unlike the shadow moiré technique.
DFP has the disadvantage of warpage resolution being dependent on field of view. For this technique a field of view of 64x48mm, generating a measurement resolution of 5 microns, was chosen.
The strengths of the DFP measurement technique include:
- Full field data acquired in less than 2 seconds
- Able to measure sudden and large height changes up to nearly 20mm
- High data point density
The DFP technique is offered as:
- A DFP module on the AXP system
- The base technology for the CXP system
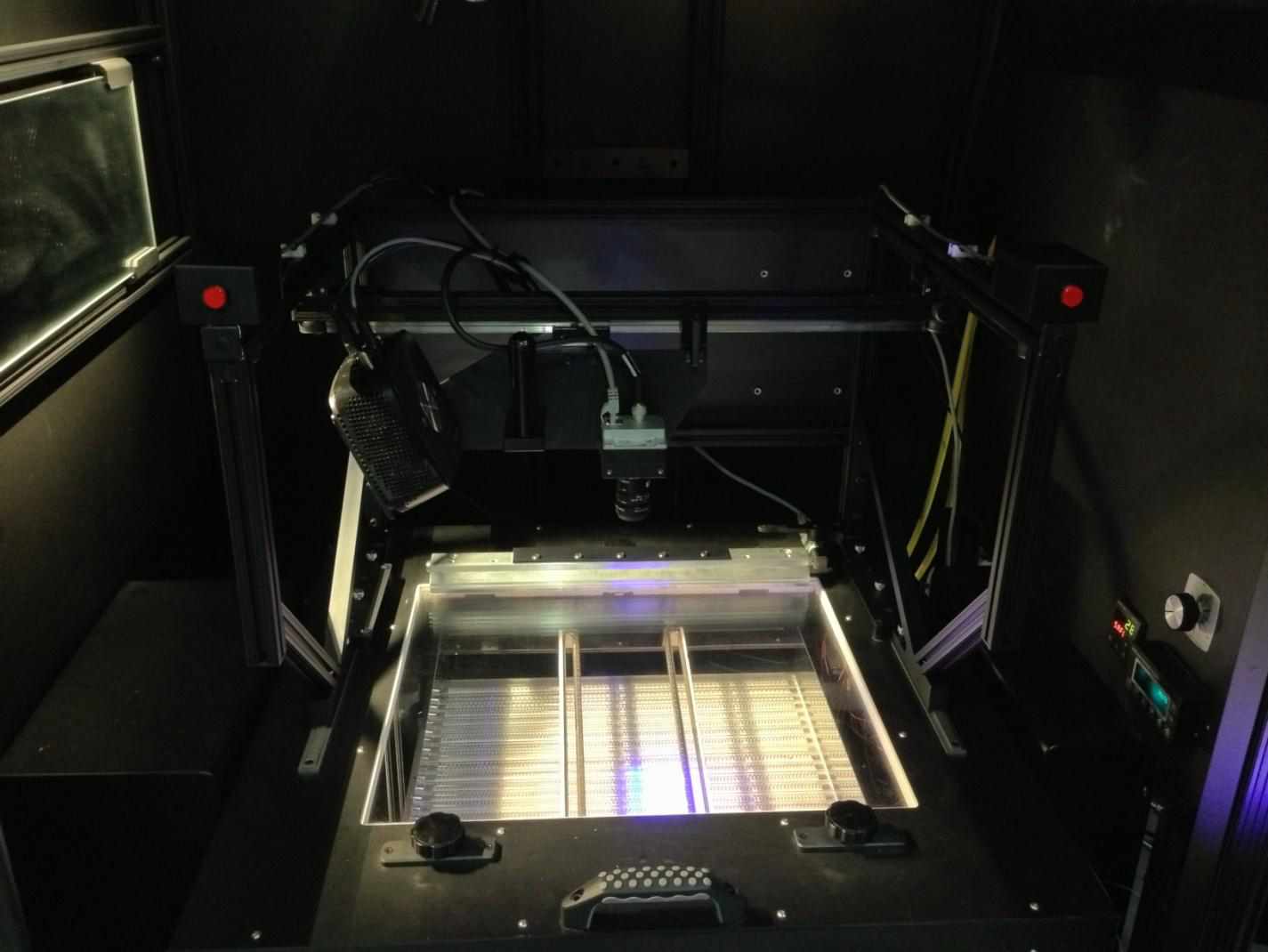