Some companies new to ESD testing approach Accelonix requesting a quotation for an ESD generator alone. However, a generator by itself cannot ensure a successful ESD test sequence. Numerous factors influence the test outcome, and the applicable standards outline additional critical details that must be considered.
This article explains why a complete ESD test setup is necessary to achieve accurate, reliable, and standard-compliant results, covering key topics such as the importance of ESD testing, the components of a complete setup, practical examples, the role of the ESD generator, and best practices for conducting effective tests.
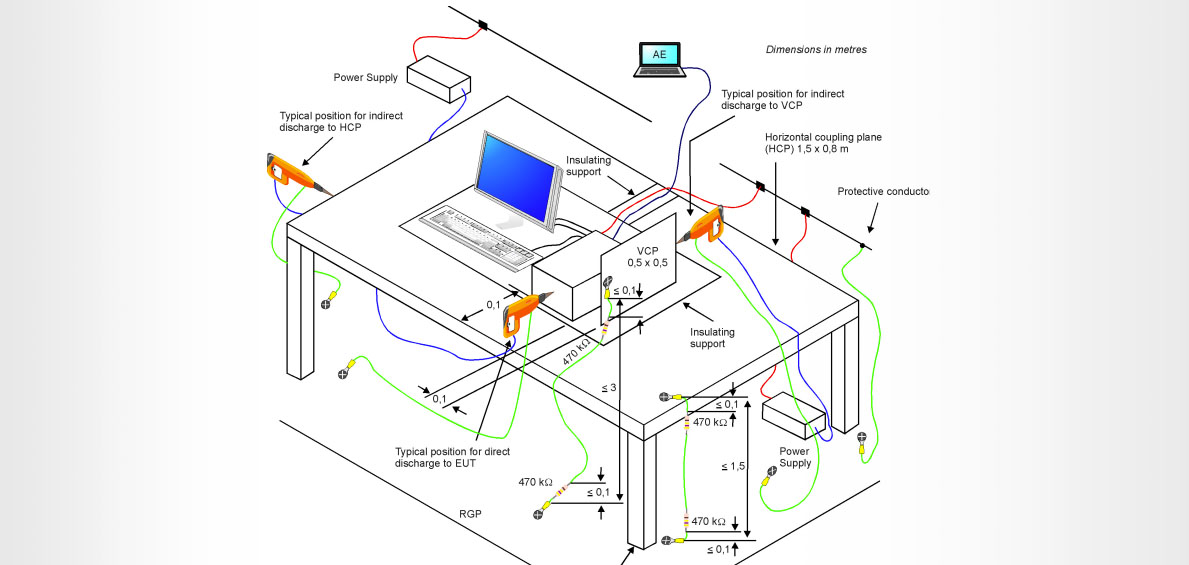
Why ESD Testing?
Electrostatic discharges (ESD) are ubiquitous phenomena that can seriously damage sensitive electronic components. In industrial and manufacturing environments, rigorous ESD testing is necessary to ensure the robustness and compliance of products against these electrostatic events. In order to perform the test, a simple test generator is not sufficient. To obtain reliable and repeatable results, it is essential to set up a complete testing environment that incorporates various complementary elements.
Electrostatic discharges can cause immediate or latent failures in electronic circuits, leading to high costs in repairs or replacements, reducing the long-term reliability of the product. International standards, such as IEC 61000-4-2 and ISO 10605, define standardised methods to test the resistance of electronic equipment to ESD by simulating real conditions. These tests ensure that products operate correctly in high-risk discharge environments, such as: factories, hospitals, research laboratories, residential or automotive environments. They are also essential for regulatory compliance and to avoid delays in bringing products to market.
The Essence of a Complete ESD Setup
A complete setup for ESD testing comprises several key elements that must work together to provide results that comply with standards. Here are the main components and their importance in a testing environment.
Horizontal and Vertical Coupling Planes
The Horizontal Coupling Plane (HCP) forms the centre of the entire test setup. Coupling planes are essential for simulating the effects of electrostatic discharges on surfaces adjacent to the EUT. The HCP is placed on the test table and has minimum dimensions of 160 x 80 cm. The Vertical Coupling Plane (VCP), typically 50 cm x 50 cm, is positioned vertically 10 cm from the EUT.
Correct installation of the HCP and VCP is crucial. Both HCP and VCP are connected to the Ground Reference Plane (GRP) via a special discharge cable. The HCP reproduces conditions where a discharge occurs on a horizontal surface near the EUT, and the VCP simulates discharges on adjacent vertical surfaces. The IEC 61000-4-2 standard specifies dimensions and installation methods to ensure test reproducibility.
Discharge Cables and Insulation
Discharge bleeder cables are essential for connecting the coupling planes to the ground plane, ensuring a controlled path for discharge currents. To limit the discharge current and in order to create distributed resistance, they must be equipped with 470 kΩ resistors at each end. These resistors are exposed to high Voltages, so an ordinary resistor won’t do the job. As Peter Green was able to take photographs during an experiment with a 3 [W] resistor and an ESD gun charged to only 8 [kV], the breakdown effects could clearly be seen.
But also the cable itself is exposed to high Voltages so it shall be isolated and have a bright colour indication (which is definitely NOT the green/yellow PE colours). So, better acquire your bleeder cable from a renown manufacture with plenty of experience in the field.. Both the HCP and the VCP have their individual discharge bleeder cable.
The Test Table
To comply with the IEC 61000-4-2 standard, the table must be 80 cm in height and carry the HCP which is a minimum of 160 cm x 80 cm. In order to avoid electromagnetic interference that could skew test results it should be made from an insulating material, such as solid wood or non-conductive plastic. Solid wood is often preferred for its robustness and insulating properties. The table shall be free of other metal components, like metal screws, nails or metal brackets. Larger dimensions may be necessary for bulky equipment or to incorporate additional tests such as burst (IEC 61000-4-4) or surge (IEC 61000-4-5). The table will be located on top of the Ground Reference Plane (GRP) and carries the HCP.
Isolation
The EUT is isolated from the HCP by insulating non-hygroscopic sheet material. The dielectric sheet should minimise impact on the electric field, while also preventing undesirable currents from skewing test results. For the IEC 61000-4-2 standard, this material is only: 0.5 mm thick. While for the ISO 10605 the material shall be between 2 and 3 mm thick.
The Ground Reference Plane
The Ground Reference Plane (GRP) on the floor plays a fundamental role in dissipating electrical charges during tests. The GRP should extend at least 50 cm beyond the HCP/test table on all sides and thus measuring a minimum 260 cm x 180 cm. The material is generally copper, aluminium or steel sheet. It serves as a ground reference for the entire setup and is connected to the protective earth. Both the discharge bleeder cables from the HCP and VCP are connected to the GRP.
Practical Examples of Complete Setups
Here are some concrete examples of setups used by clients in various sectors, demonstrating the importance of a complete setup for successful ESD testing.
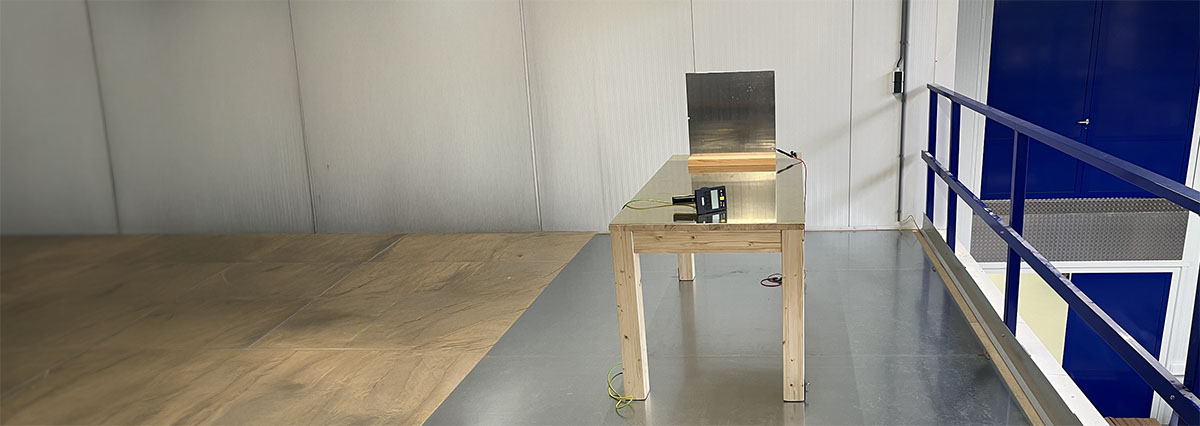
Example of Setup 1
Customer has no experience or background in EMC or ESD testing. Hence, this project starts from scratch. The only things required, were some space and a flat floor.
- Ground Reference Plane (GRP): Durable sheet metal measuring 260 cm x 180 cm, connected to earth.
- Test Table: Made of solid wood, dimensions of 160 cm x 80 cm x 80 cm.
- Horizontal Coupling Plane (HCP): Durable metal plate, dimensions identical to the table.
- Discharge Bleeder Cable: High voltage with 470 kΩ resistors, type EAS 30-1.5.
- Vertical Coupling Plane (VCP): supplied as a ready to use set, including: A wooden stand that also serves as a spacer, knob for easy connecting the generator’s discharge tip and Its own EAS 30-1.5 special high Voltage bleeder cable.
- Insulating foil: of 0.5 mm
- ESD Generator: EM-Test Dito set. Compliant with IEC 61000-4-2 and ISO 10605, capable of discharges up to 15 kV.
- Full installation and demo: Ensuring the correct details are applied, functioning of the setup verified and user immediately up to speed for testing.
- Results: Ensures compliance with standards and enhanced protection of sensitive electronic components. User immediately up to speed for full-compliant testing.
Example of Setup 2
Customer is familiar with EMC and ESD testing at intermediate level. There were already various provisions available. Their Equipment Under Test (EUT) can get very warm.
- Ground Reference Plane: The tests will be performed in the Faraday chamber which was supplied before. The chamber floor forms the GRP.
- Test Table: Solid wood enlarged to 200 cm x 80 cm to accommodate large EUTs.
- Horizontal Coupling Plane (HCP): Durable metal plate, dimensions identical to the table.
- Discharge Bleeder Cable: High voltage with 470 kΩ resistors, type EAS 30-1.5.
- Vertical Coupling Plane (VCP): supplied as a ready to use set, including: A wooden stand that also serves as a spacer, knob for easy connecting the generator’s discharge tip and its own EAS 30-1.5 special high Voltage bleeder cable.
- Insulating foil: of 0.5 mm
- ESD Generator: A 30 kV] Teseq NSG 437 is already available at the customer’s facilities. Accelonix ensures the generator and its discharge networks are functioning according to the specs by means of an accredited calibration.
- Full installation and demo: Ensuring the correct details are applied, functioning of the setup verified and user immediately up to speed for testing.
- Results: Ensures compliance with standards and enhanced protection of sensitive electronic components. User immediately up to speed for full-compliant testing.
The Role of the ESD Generator
An ESD generator is merely part of the entire test-setup. Nevertheless, its functioning is key for simulating electrostatic discharges. These discharges shall be compliant to the applicable standard. These standards describe the waveform by means of rise times and durations. The waveform is mainly determined by the generator’s (interchangeable) discharge network.
Other parameters are charge Voltage (at least 15 kV), possibility of testing in both positive and negative polarity, adjustable repetition frequency and interchangeable discharge tips. Examples of extra options are charge indicator, discharge trigger type, internal safety bleed-off resistor, programmable functionality, battery or cable powered.
Best Practices for ESD Testing
To guarantee the reliability and reproducibility of ESD tests, it is important to follow certain best practices. Environmental control is essential. To avoid variations in result, stable ambient temperature conditions and maintaining relative humidity between 30% and 60%, as humidity affects electrostatic discharges. Preparation of the EUT should include conditioning to allow the EUT to acclimatise to test conditions and configuration where the EUT is in normal operating condition during tests.
The test sequence should comprise direct discharges applied directly to accessible points of the EUT and indirect discharges via the coupling planes to simulate environmental effects. Documentation is crucial, with detailed reports recording all test parameters, observations and results, and analysis of results to identify weak points and propose design improvements if necessary. To avoid accidents, safety should not be overlooked. When tests are in progress, follow safety procedures and signalling to personnel and keep distance from the: EUT, cabling, HCP and VCP.
Conclusion
ESD tests cannot be successfully conducted without a complete setup that complies with international standards. It is essential to incorporate not only a high-performance ESD generator but also an insulated test table, compliant ground and coupling planes, and high-voltage discharge cables to guarantee reliable and reproducible results.
An incomplete setup can lead to ineffective tests and high costs due to non-compliance or the need to retest products. By investing in a complete setup and following best practices, companies can ensure that their products are protected against the dangers of electrostatic discharges. This not only improves the quality and reliability of products but also strengthens the confidence of customers and business partners.