The APT-2600F series is a high-performance flying probe test system featuring 4 heads with 6 probes on the top and 2 heads with 4 probes on the bottom, allowing simultaneous dual-sided testing.
This setup improves test coverage, reduces test time, and eliminates the need for board flipping, lowering the risk of damage.
With models supporting large PCB sizes and automation, it provides a cost-effective solution for prototype to mass production, enhancing PCB assembly quality.
All models are available as inline machines. By connecting with a loader/unloader (available at Accelonix), you can build a continuous automatic test line with a maximum speed of 40 m/min. This allows for a smooth production line and efficient board inspection.
It provides an optimal in-line inspection environment for your manufacturing process, helping to achieve both productivity and quality control.
Goepel Takaya Boundary Scan Integration 
TestWay Express is a fully integrated solution that enables electronic manufacturers to optimize the design to delivery flow by: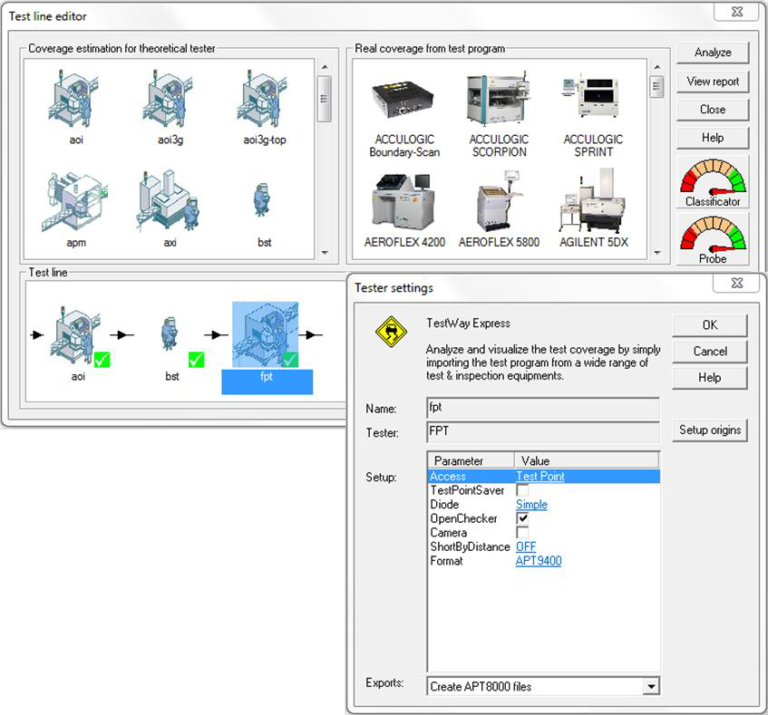
- Defining the manufacturing line; including a combination of assembly, inspection and test machines.
- Placing test probes intelligently to maximize the coverage and minimize the fixture costs, both initially and in the event of required modifications.
- Estimating the test coverage for each individual strategy using theoretical models and optimize the combined results.
- Generating input files for each test stage that reflects the test options for the selected strategy.
- Measuring the real test coverage by importing the post-debug test program or coverage data.
- Comparing the early estimation with the actual measured test program coverage, identifying gaps in the overall strategy.
The capability to generate lean test programs has particular benefits for the Takaya flying probe tester by:
- Reducing debug time: Machine capability models, automatic test creation algorithms, optimum probe angle selection methods and advanced circuit analysis work together to reduce the amount of machine debug time required after output, thereby increasing machine capacity.
- Increasing Test coverage: Push through technology allows automatic simple cluster testing to increase test coverage through low value resistive components.
- Reducing engineering effort: Automatic component modelisation and intelligent opportunity assessment work together to save engineering time.
- Increasing machine speed: Advanced circuit analysis algorithms allow the creation of tests to target the failure opportunities with no superfluous tests.
- Reducing machine workload: Powerful test coverage analyzers work within the machine capability models to allow the optimization of combined tests across multiple machines, in order to achieve a lean test strategy.
Click here for more information.
APT-2600F Brochure: please contact us!